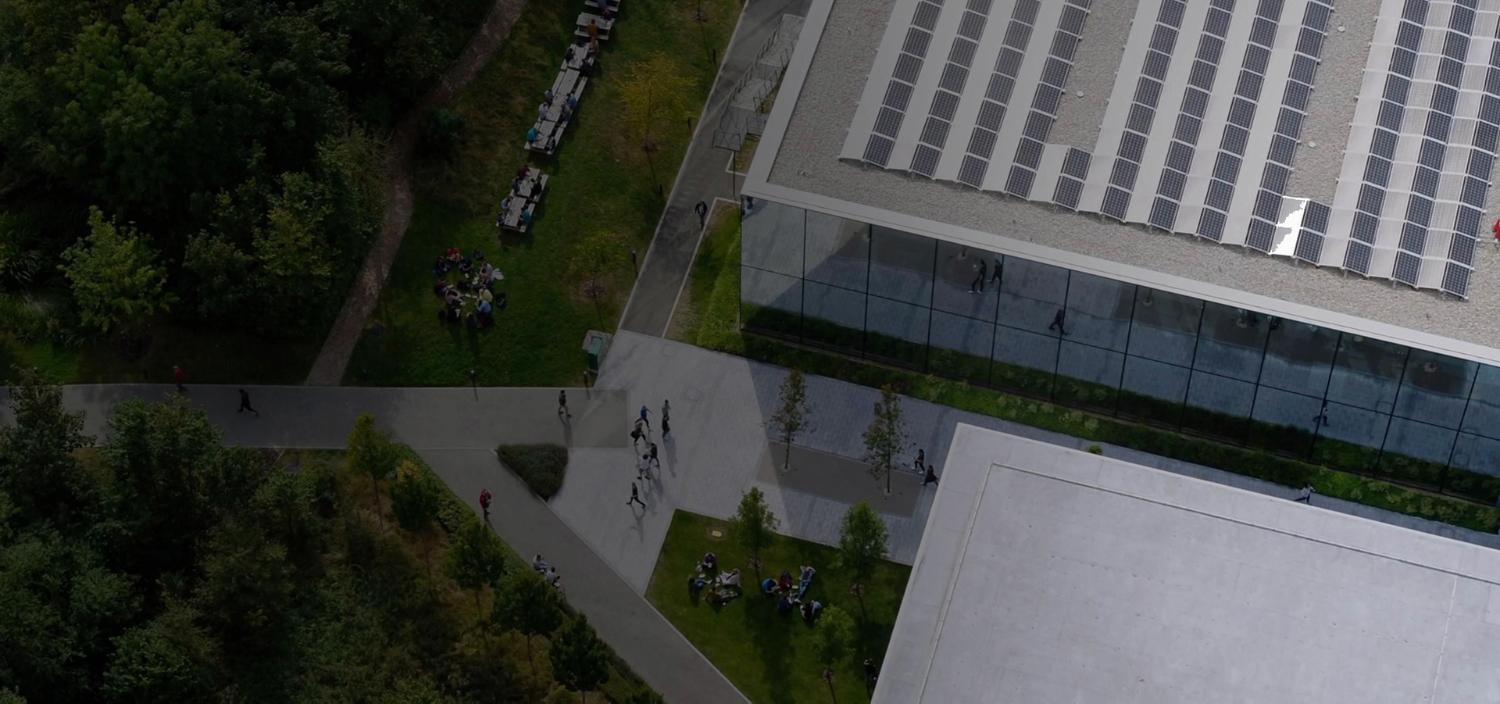


Investing in a better future
-
Engineers invent technology to solve tomorrow’s problems
They’re crucial not just to the future of Dyson, but to the world. Technology ambitions demand a ready supply of the brightest engineers, and a shortage of talent is holding advancements back. That's why we set out to transform education, with the Dyson Institute.
-
Promoting change to young inventors
The James Dyson Foundation is Dyson's engineering education charity. It introduces budding inventors to the exciting world of problem solving.
-
Advancing medical and scientific research
The James Dyson Foundation funds a dementia research Fellowship, in partnership with Race Against Dementia. Dr Claire Durrant analyses brain samples on a microscopic level, using in-house equipment and expertise at Dyson's labs in Malmesbury.
-
The JDF funds a dementia research Fellowship¹
-
Approximate number of Dyson Institute Undergraduate Engineers²
-
Awarded to the James Dyson Award Sustainability winner each year¹

Using technology and ingenuity to farm responsibly and at scale
-
Our circular farming system
We feed crops into our anaerobic digesters, which generate renewable energy. Heat from the process is piped into our glasshouse to encourage fruit growth. In the future, the biogas will be captured to convert into biofuel for vehicles.
-
Renewable power
Dyson Farming produces enough renewable energy to power the equivalent of 10,000 homes. Renewable energy production represents a huge opportunity to do more with the resources available to us.
-
Using technology to improve harvests
We use harvested rainwater and excess heat from our anaerobic digesters in our 6-hectare¹ greenhouse, to grow strawberries out of season. And help reduce the food miles associated with imports.
-
Hectares of energy crops harvested annually³
-
MWh renewable energy produced per year³
-
Tonnes of strawberries grown each year³
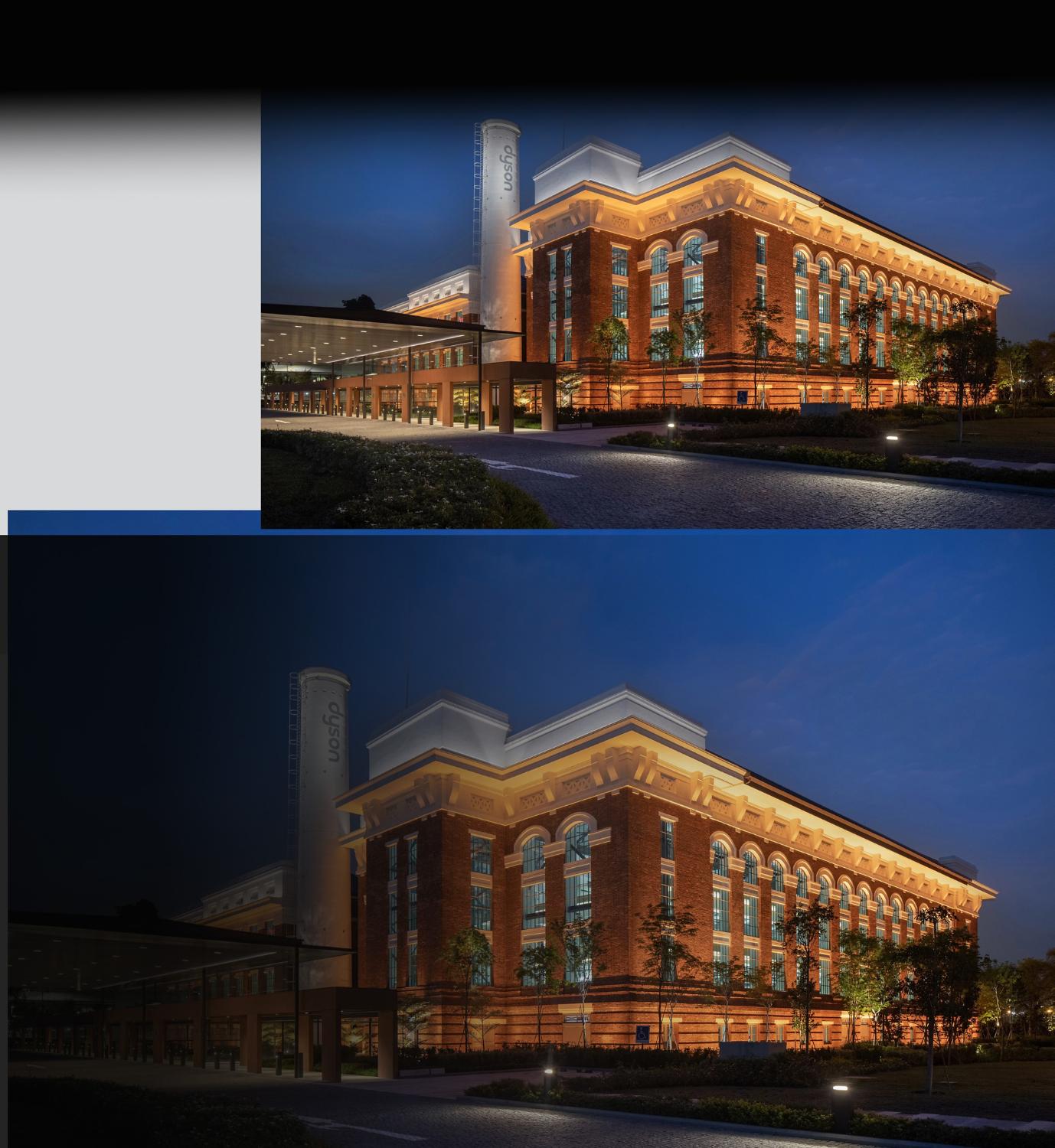
Our headquarters, campuses and manufacturing
-
Our sites use renewable energy
By the end of 2022, 100% of Dyson-owned manufacturing, and 65% of the electricity consumed by Dyson spaces globally, was renewable or covered by Renewable Energy Guarantees of Origin certificates.
-
St James Power Station
We restored St James Power Station in Singapore using environmentally friendly materials, while optimising energy efficiency and procuring renewable electricity.
-
Malmesbury campus
Our UK RDD building is equipped with solar panels – contributing towards powering the building. A ground source heat pump under the car park saves energy by regulating the temperature inside the Lightning cafe – and keeping our IT server centre cool.
-
Of Dyson-owned manufacturing uses renewable energy⁴
-
Solar panels above spaces in our Malaysia Development Centre car park
-
The year we painstakingly restored our Hullavington campus
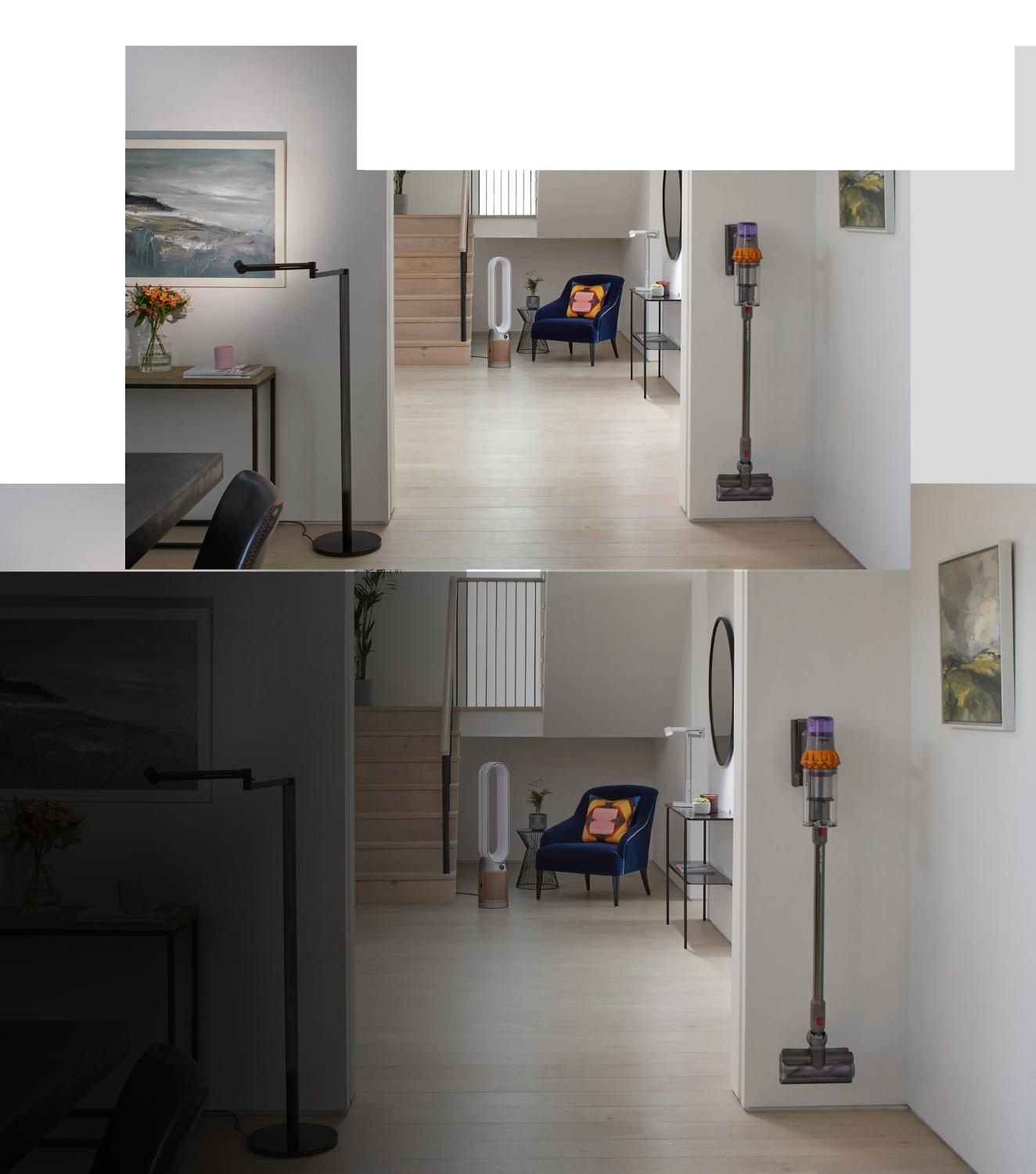
Pioneering core technologies, to do more with less
-
A revolution in bagless vacuum cleaners
In 1993, we engineered the Dyson DC01. A vacuum that separates dust from air using centrifugal forces – overcoming the inefficiency and poor performance of traditional machines. With no need for bags. Others followed, making vacuum bags a thing of the past.
-
Reinvented motors
Standard brushed motors are heavy, clunky, and consume more electrical energy. So we set out to engineer one that worked better. The result was the Dyson digital motor, which has allowed us to develop new technologies in multiple categories.
-
Engineered with energy efficiency in mind
The Dyson Airblade 9kJ hand dryer, when in Eco mode, produces up to 99% less CO2 emissions than paper towels. And with 337mph sheets of air to dry, it uses just 13% of the energy of hot air hand dryers.
-
We released our first vacuum made from recycled plastic
-
Of the plastic in the Dyson HEPA Purifier Cool™ Formaldehyde purifying fan's filter frame is recycled
-
Years is how long light quality is protected for in Dyson lighting, with Heat Pipe technology cooling high-power LEDs.⁵
-
Products and technology sustainability magazine
Read more stories about our journey towards sustainability.
-
Renewed Dyson technology
Our machines are built to last, which minimises the need for them to be replaced or recycled. Refurbishing a machine increases its lifetime, reducing the need for new parts and raw materials.